Friday, October 27, 2006

Spraying cellulose insulation into the wall cavities. It looks like a dirty job, and it is! One guy sprays the insulation into the walls and it seems about half of what is sprayed drops to the floor. The second guy has a large vacuum hose and his job is to vacuum up all the insulation off of the floor. The insulation blowing machine is set up to recover this material, add new cellulose, and send it back for another trip. A third crew member has a rubber roller gizmo which lightly scrubs the bulky cellulose down to the plane of the wall studs. The 3 of them just keep working in a big gray cloud of dust.
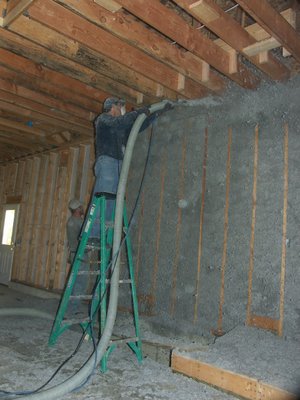
More shooting of insulation. The cellulose insulation is blown through the gray tube and out a large diameter nozzle which has two water nozzles (one on each side) spraying into the stream of cellulose to lightly wet it. Starch in the cellulose acts as a glue to give the mass some cohesiveness and hold it in place. That's not to say the insulation is "'glued in" - one could walk up after spraying or now (days later) and pull the insulation right out.

As part of the insulation prep work, the contractor foams behind all the electrical boxes in exterior 2x4 walls. This has to be done because the way/direction the cellulose insulation is sprayed doesn't do a good job of filling the narrow gap between the box and the sheathing behind. These are 3 of the 25 electrical receptacles in the garage!
Thursday, October 12, 2006
Monday, October 09, 2006

The business end of about 4,000 feet of cable in the basement. And, there's still some more basement wiring to run! The blue, white and black cables to the right are the 'structured wiring' runs for cable TV, computer and telephone and which will end up in their own panel. The yellow wires to the left are the security system cables and will terminate in two wall-mounted panels.


The kitchen range hood exhaust duct with the open end bagged to keep insulation out of it and temporarily set off to the side over the garage (where the insulation will be shallower). To the far right is the plumbing vent for this end of the house and mid-left is the lift-beam over the garage stairway.